In the new world of recession economics, where “return on investment rules,” how do all the pushes for green homes make any sense? Well, when it comes to the ENERGY STAR part of the equation, which is 60% of LEED or any other green program, it pays in spades. You must go Blue before you can go GREEN. Why? ESLH program is the first time building science has been applied to residential construction. Building Science is the study of how all the components of a residence react with each other. For example, if we slow down natural air flow (drafts), install in Low E glass windows, increase the R-value in the walls, floors and ceilings, we can effectively reduced the amount of heating and cooling necessary to keep the house comfortable. Combine this with high efficiency air conditioners and heating systems, and now we are making a real difference in the operating cost of this house. In the case of “The Bluffs at Eaton’s Neck,” where the houses will range between 5,000 and 6,000 square feet, these people will enjoy an average savings of $4,000 annually in energy cost above the same house not built to the ESLH guidelines. If that’s not enough to start building ENERGY STAR, the increased comfort levels in these homes are remarkable. The temperature range from one end of the house to the other is no more than three degrees. We control where the fresh air comes into a house with balanced air systems. These systems pull air from bathrooms and kitchens where moisture accumulates and exhaust it outside, while drawing outside air and place it into the return ducts for conditioning.
ESLH MOTTO IS “BUILD IT TIGHT, VENTILATE RIGHT”
ESLH houses are healthy homes and are tested in ways like never before, to make sure all of the components of the house are working according to design. Duct systems are tested for leaks, boilers are tested to ensure they meet design efficiency. The whole house is tested for drafts. When natural gas is in the house, this is tested right to the combustion appliance to ensure no gas leaks happened during installation. Last, but far from least, is reduction in carbon dioxide, sulfur dioxide and nitrogen oxides of our sample home in Eaton’s Neck will have an estimated combined reduced carbon footprint of 10 tons annually.
Now how much did all this cost? Well, prices vary from job to job as well as the variables of residential habits such as the temperatures you feel comfortable in and the hours of electronics being run. This makes it difficult to give a true ROI, but these improvements rarely add more than $15,000 to the cost of construction. Then, subtract the cost savings coming from the reduction in air conditioners needed, add utility rebates and federal tax credits, and your ROI is under three years. As we transform the market place, and all these unique practices become common place, the prices will come down. Therefore, further reducing first cost (historically our estimated savings have been 10% higher than actual savings). Now, even the biggest skeptics question why we have waited so long to include these changes in our new home construction.
The simple answer is yes, but “how much?” would be the follow up question. Where is the air coming from? This along with other long standing beliefs will be discredited into the category of “what were we thinking back then, because it was not energy conservation?” Building science tells us air flow within the conditioned space of the house is critical to a healthy living environment, but air flow behind the walls helps no one and reduces the R- value of the fiberglass insulation to almost nothing. Back in the 70’s, during the first oil embargo, there was a rush of home improvement ideas such as placing a vapor barrier over the studded walls just prior to sheet rocking. Bad idea, because the air was not coming from the conditioned side of the house but from the outside and creating a moisture barrier trapping moisture behind the walls. This mantra has allowed sloppy workmanship to be tolerated. I have walked through newly framed houses today and was shocked to find air gaps in framing that would allow constant air flow behind the walls.
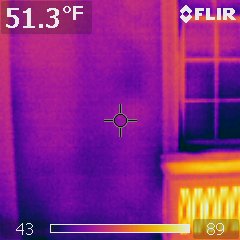
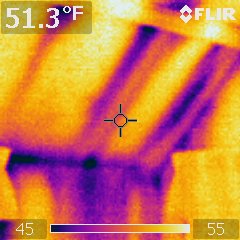
Go to the outlets or wall switches within your own home during the winter months, place the back of your hand next to them, and feel the cold air that flows down the wall and spills out wherever it can. This happens because cold air is heavier the warm air and flows like water down your walls. Is this how you want your house to breathe? Here are some infrared pictures which illustrate how this happens along with some framing nightmares.
A good rule of thumb when deciding where to foam air seal a house will always be the between the conditioned space and unconditioned space.
Example: if your attic is an unconditioned space, place a bead of caulk on the entire top plate. Sheetrock will stop the cold attic air from falling down the walls.
In an effort to reduce the demand of foreign oil into the US government, we looked closely at where this oil was being used. Residual energy was about 40 percent of the use. In addition, here on Long Island, most of our power plants are fueled by foreign oil. So every time we save on our electric bill, as well as our heat oil, we are effectively reducing this demand. In 1990, the ENERGY STAR Label was born and designed specifically to take on these tasks. Save energy, save money, increase comfort. When these programs first came out, ESLH felt comfortable stating a 30 percent reduction in operating cost to the owner. Great! But now that that homes have been built, we see over 40 percent in most new homes.
In 2011, Energy Star Labeled Homes raised their bar to include other areas of concern such as moisture control and HVAC contractor certification. There was a fair amount of push back from the construction community because of the additional cost for compliance while the country was in a very weak housing market. After meeting with the powers that be, we have a tiered program (ie. Gold, Silver, Bronze). ESLH clearly states that you either achieve the Energy Star status or you don’t. Hence, HERS House is born, just the old ESLH version. HERS stands for Home Energy Rating System.
Things have changed for the better in this market and we owe it all to the solar pioneers. They paid big bucks for the early version photovoltaic panels with little payback. The problem is the panels only produce Direct Current (remember back to 6th grade science ) or DC, as it’s called. All the appliances need Alternating Current or AC to run. So inverters are needed to convert this current to use house current. After the conversion, very little was left from the panel’s output for consumption. With all the rebates available to the end user, you still had a ten year ROI. Not exactly for the people who were looking to save some money off their utility bill. Good news is they have gotten much more efficient, along with a decrease in pricing. I have clients who have told me their ROI is closer to 5 years.
YES, The New York State Building Code does have an Energy code requirement that mirrors the HERS code. Instead of modeling with a HERS scoring software you can use the DOE version called RESCHECK. State code does reference HERS scoring where you can achieve a passing score. (R406.1) Energy Rating index (ERI) of 62 or less. This index is usually sored using a HERS modeling program, such as REM-RATE. Blower doors and Duct leakage testing to outside are mandatory in the state code. They are also impossible to pass without making a conscious effort during the construction process to foam, caulk and air seal framing and all duct work. Manuals J, S & D are also mandatory and many towns require this prior to permit. (see definition)
You sure can. I find when a house uses Spray foam to insulate from basement to roof they create an air barrier with little air changes taking place. The upside is they take very little energy to heat and cool . But we would be creating terrarium and things will start to get wet in a hurry. Now that we know this at the start we can address it. Fresh air ventilators are installed instead of bath fans along with an automatic timer by doing this you now know exactly where and how much air is coming into the home. You control it. If you’re a person who likes to have windows open when weather permits, this is never a problem but in the winter months you may need the fresh air to be mechanically vented.
When the EPA rolled out the ENERGY STAR Labeled Homes program (ESLH) they touted a 30 % savings as achievable. After 10 years of building to the ESLH standards we find the original estimates to be very conservative. Home Energy Solutions did some interviews with former clients to see what their actual savings have been. To our delight, all of the clients reported higher than anticipated saving in not only in dollars but comfort as well. 50% saving is not only possible but real. These people will save every day of every year for the life of the house.
The Air Conditioning Contractors of America (ACCA) developed software programs called manuals J, S and D that identify every heating and cooling load for every room in your residence. Manual J is Identifies the loads based on outdoor and indoor temperatures. Manual S selects the model of the equipment that best meet the loads the J identified. This is why we tell our clients “you pick the make you like and we pick the model”. Manual D takes all the information from the J & S and Designs a Duct layout over your floor plans. It ensures that the correct velocity of air hits the diffuser grill in order to evenly spread the conditioned air into each room. These manuals can be used as bid specifications when selecting an HVAC contractor in order have all the bidders giving you a proposal for the same equipment.